Usually, evidence of the costly results (financial, injuries, wasted productivity, missed deadlines, frustration, opportunity costs, etc. ) of poor documentation do not make into the media's search light.
It's so routine.
And poor documentation is not sexy or sensational enough to attract the attention of a digital or paper journalist or celebrity.
This $6.7 million United States Air Force mistake was so costly it attracted a reporters attention (see below).
This $6.7 million United States Air Force mistake was so costly it attracted a reporters attention (see below).
It is worth reading for the lessons it offers, including the positive spin the USAF spokesman puts on this fiasco at the end of the piece.
He's not alone in this, unfortunately, which is one reason poor documentation continues despite the widespread costs.
Whoops! There goes $6.7 million
At Hill AFB: A 5'' safety pin shoots down an F-22 engineA piece of metal - 5 inches long and of minimal cost - caused $6.7 million in damage to the engine of an F-22 fighter jet at Hill Air Force Base. Air Force officials say it was the most expensive mishap since the next-generation fighters began being deployed to operational squadrons last year.
Good Documentation Saves Money and Increases Profits
Reuters News Service once carried a story* about the International Space Station crew getting a difficult start because the written procedures the crew carried into orbit were not entirely reliable. This is NASA’s careful way of saying the setup procedures were so poorly written that the crew could not do their job.
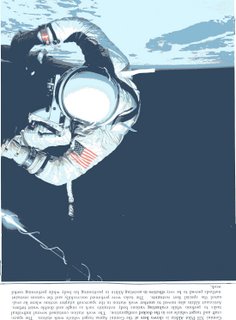
Service engineers and maintenance technicians are able to keep the tool operating longer
Along with so many other factors, first-rate documentation assures that better tools are built and sold. In turn, this leads to satisfied customers, more tool sales and higher profits.
Whoops! There goes $6.7 million
At Hill AFB: A 5'' safety pin shoots down an F-22 engineA piece of metal - 5 inches long and of minimal cost - caused $6.7 million in damage to the engine of an F-22 fighter jet at Hill Air Force Base. Air Force officials say it was the most expensive mishap since the next-generation fighters began being deployed to operational squadrons last year.
The accident occurred Oct. 20, when the Air Force's first Raptor squadron, based in Langley , Va. , was at Hill for an inaugural training deployment.
A 22-page investigative summary, released this week, concludes the engine was damaged when a mechanic failed to remove a safety pin from the plane's forward landing gear.

Just after the pilot, Maj. Evan Dertien, had started the Raptor's twin 35,000-pound-thrust engines, Senior Airman Arthur Blosser noticed the pin was still installed. Blosser signaled for Dertien to shut down the left engine so that he could approach and remove it.
As Blosser removed the pin, the streamer attached to it was caught in the jet intake of the Raptor's right engine, ripping the pin from his hand and sucking it into the engine.
Dertien, according to the report, "heard a crunch and a winding down sound" as witnesses outside the aircraft "saw sparks coming from the engine."
"For this particular accident, the dollar amount of the damage to the right engine is approximately $6,754,275," said Air Force spokesman Lt. Daniel Goldberg.
The cost of a landing gear pin, Goldberg said, "is minimal."
Investigators concluded that, while Air Force guides correctly instructed Raptor mechanics to install the landing gear pins before performing maintenance on the airplanes, there were no similar step-by-step instructions to ensure mechanics remember to take the pins out prior to clearing the aircraft for use.
Critics have said the Raptor program - at one time planned to cost $35 million per aircraft but at times since has approached $200 million per unit - is too expensive and largely irrelevant to modern war-fighting needs.
That, however, did not diminish the excitement at Hill in October when the Langley squadron arrived for two weeks of flying. On Oct. 18, the squadron's commander, Lt. Col. Jim Hecker, dropped the first bomb from a Raptor over the Utah Test and Training Range .
Hecker later called the time spent at Hill, where dozens of Raptors will be maintained at the Ogden Air Logistics Center , invaluable.
Good Documentation Saves Money and Increases Profits
Reuters News Service once carried a story* about the International Space Station crew getting a difficult start because the written procedures the crew carried into orbit were not entirely reliable. This is NASA’s careful way of saying the setup procedures were so poorly written that the crew could not do their job.
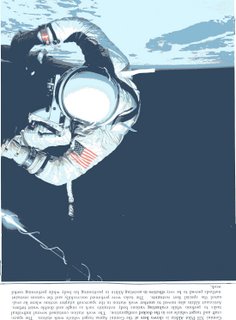
Space Station Crew Getting a Slow Start the article states:
CAPE CANAVERAL –– The crew of the International Space Station has a toilet, a food warmer and videoconferencing technology, but it is running short on oxygen… The problem is that a few things have fallen through the cracks, Jeff Hanley, lead flight director for the NASA portion of the mission, said Friday. Not literally, of course. Nothing falls in the weightlessness of space, but the written procedures the crew carried into orbit have not been entirely reliable. That led Shepherd to advise his bosses Friday at NASA Mission Control, "We worked really hard yesterday, and we could not keep up with the timeline. We're way behind today, too.
How many can identify with the astronaut’s frustration when trying to set up a critical hardware sub assembly or to use software only to find that the procedures…have not been entirely reliable?
Hopefully…not many… because if the technical writers produce first-rate electronic and paper documents that are in plain English: clear, concise and consistent.
By doing so, technical writers contribute to the profitability of products in these ways:
Electrical, mechanical, design, and software engineers can build the tool more quickly Manufacturing engineers and technicians are able to build tools faster
Installation engineers are able to install the tool faster (avoiding the astronauts problems) Training personnel are able to educates those who use the tool more quickly Electrical, mechanical, design, and software engineers can build the tool more quickly Manufacturing engineers and technicians are able to build tools faster
Service engineers and maintenance technicians are able to keep the tool operating longer
Specifically, how do technical writers contribute to the bottom line?
Although most people know that technical writers produce manuals, technical bulletins, online help, and other paper and electronic documentation, others may not fully understand what else is involved in being a technical writer.
Although most people know that technical writers produce manuals, technical bulletins, online help, and other paper and electronic documentation, others may not fully understand what else is involved in being a technical writer.
What follows is an effort to explain briefly what technical writers are and what we do.
- Transforms disorganized data into communication that transfers knowledge from the subject matter expert (SME) to the customer.
- Converts the raw material of ideas into text that transfers knowledge.
- Makes effective use of communication fundamentals to develop better documentation.
- Understands the personal factors that affect communication.
- Stays current about best practices, current tools, shifting technology and data that impact technical communication.
- Knows and uses alternative methods when necessary to reach a variety of customers.
- Writes documentation in plain English for domestic and overseas customers. Makes technical documentation easy-to-read and easy-to-use.
- Remove irrelevant detail from the documentation to make it clear to the customer.
- Makes suggestions that improve…does not demand changes without a good reason
- Writes as a generalist or specialist as the need dictates
- Learns highly technical concepts to better communicate them.
- Keeps current as a technologist in a variety of applications, methodologies, and tools.
- Exercise the skills, experience, and knowledge that add value to any software, hardware and Web projects, such as usability testing.
- A technical writer can only accomplish first-rate documentation with the contributions and cooperation of all the various engineering and technical subject matter experts.
He or she must transform your technical knowledge into plain English for internal and external customers.
For all the experts who help with that job, I say thanks.
*Space Station Crew Getting a Slow Start, Reuters News Service, Sunday, November 5, 2000; Page A08